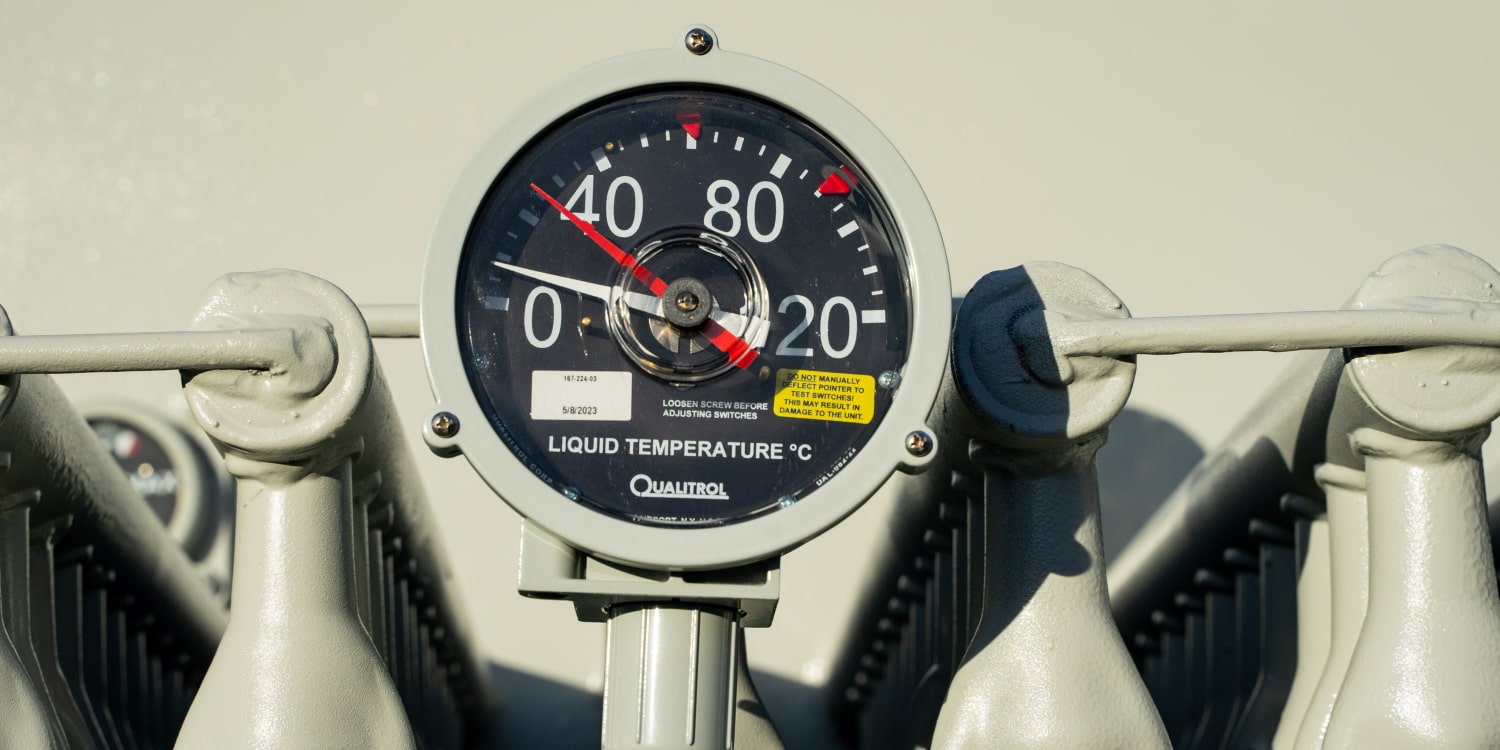
All transformers produce heat under normal loading conditions. Heating depends on the outside ambient temperature, loading, and the transformer type/design. A transformer’s thermal capabilities determine how much load it can carry. To understand the thermal capabilities of transformers, we need to understand temperature ratings.
kVA and Temperature Ratings
The nameplate kVA usually represents the threshold of the transformer’s thermal capabilities. Exceeding it could result in damage and loss of life to the unit. The rated kVA accounts for the following factors:
- Ambient temperature
- Transformer load
- Average winding temperature rise
- Hottest-spot winding temperature
- Insulation thermal class
Ambient Temperature
This is the temperature of the environment surrounding the transformer. At no load, the temperature of the windings will be similar to outside ambient levels. The average ambient temperature rating for dry and oil-filled transformers is 30°C (40°C max). This plays a key role since it contributes to the total temperature of the unit under full load.
Transformer Load
The transformer load determines how much of the transformer’s rated capacity (kVA) is being used. The temperature of the transformer is directly proportional to the amount of load applied. The transformer load helps determine the average temperature of the windings.
Average Winding Temperature Rise (AWR)
Temperature rise represents the average temperature of the hottest winding. It is listed on every transformer nameplate. The temperature rise rating is given above ambient (30°C). The temperature rise rating is configured for the nominal kVA.
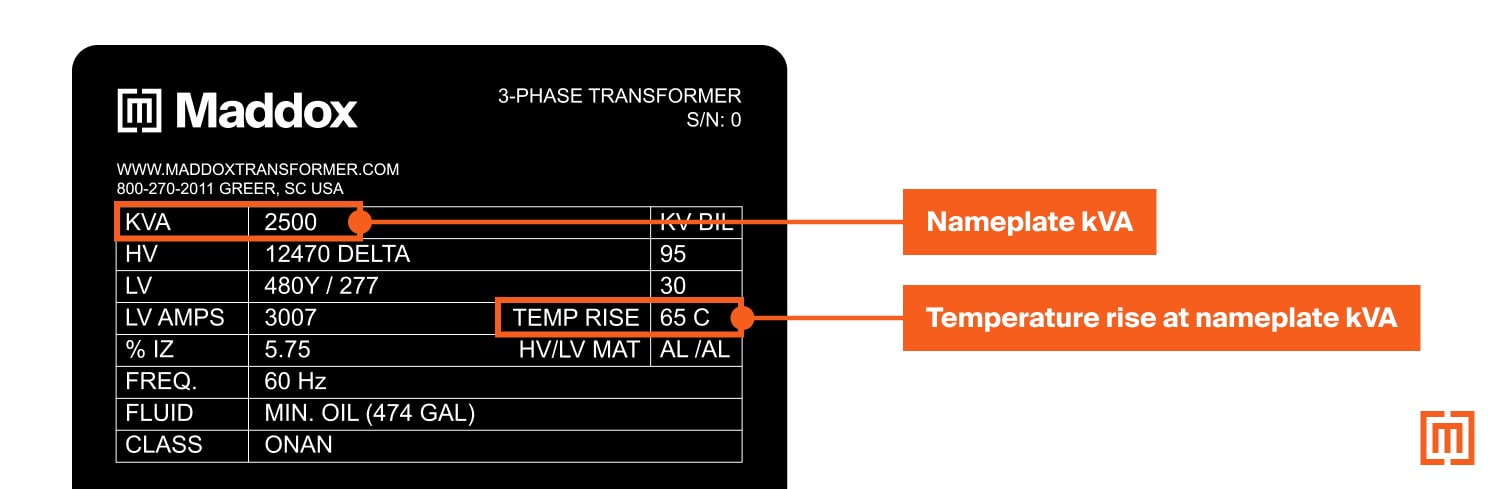
Hottest-Spot Temperature (Temperature Index)
A transformer’s coils do not heat evenly. Sections closest to the core may heat faster. Areas nearer the external cooling surfaces may heat slower. The hottest-spot (or hotspot) temperature takes this into account. It references the hottest insulated conductor in the winding. This value does not appear on a transformer’s nameplate like the temperature rise. It is established by industry standards.
Hottest-spot (Hot spot) allowance
Local hotspot measurements in the windings are difficult to measure. So, the industry has standardized hotspot allowances for various temperature ratings. The hotspot allowance is given above the average winding temperature rise. The hottest-spot temperature is the sum of the ambient temperature, temperature rise, and hotspot allowance.
The hotspot temperature in the windings is key in determining transformer lifespan.
Insulation thermal class
The temperature rating of a transformer’s insulation determines its insulation class. Exceeding the temperature rating of the insulation decreases transformer lifespan. Here are the most common insulation classes:
Each insulation class may use various materials to achieve its thermal rating. We’ll take a look at oil-filled and dry-type transformer insulation materials.
Oil-filled Insulating Mediums
Oil-filled transformers use two insulating mediums to achieve their temperature ratings. The combination of liquid and solid insulating materials determines the insulation class.
Solid
Neutral Kraft Paper
Neutral kraft paper is a cellulosic insulation made from kraft wood pulp. It insulates electrical conductors in liquid filled transformers. Electrical grade cellulose paper is tested and certified according to industry standards. This ensures high performance for electrical applications. Transformer’s using neutral kraft paper are built with a 55°C temperature rise. 55°C temperature rise units with neutral kraft paper offer an insulation class rating of 105°C.
The word kraft comes from the German word for strong. Kraft/cellulose paper is a strong insulator. Yet, it will break down at extreme temperatures. The strength of cellulose insulation is measured by its degree of polymerization (DP). New transformer insulation offers a DP between 1,000 and 1,500.
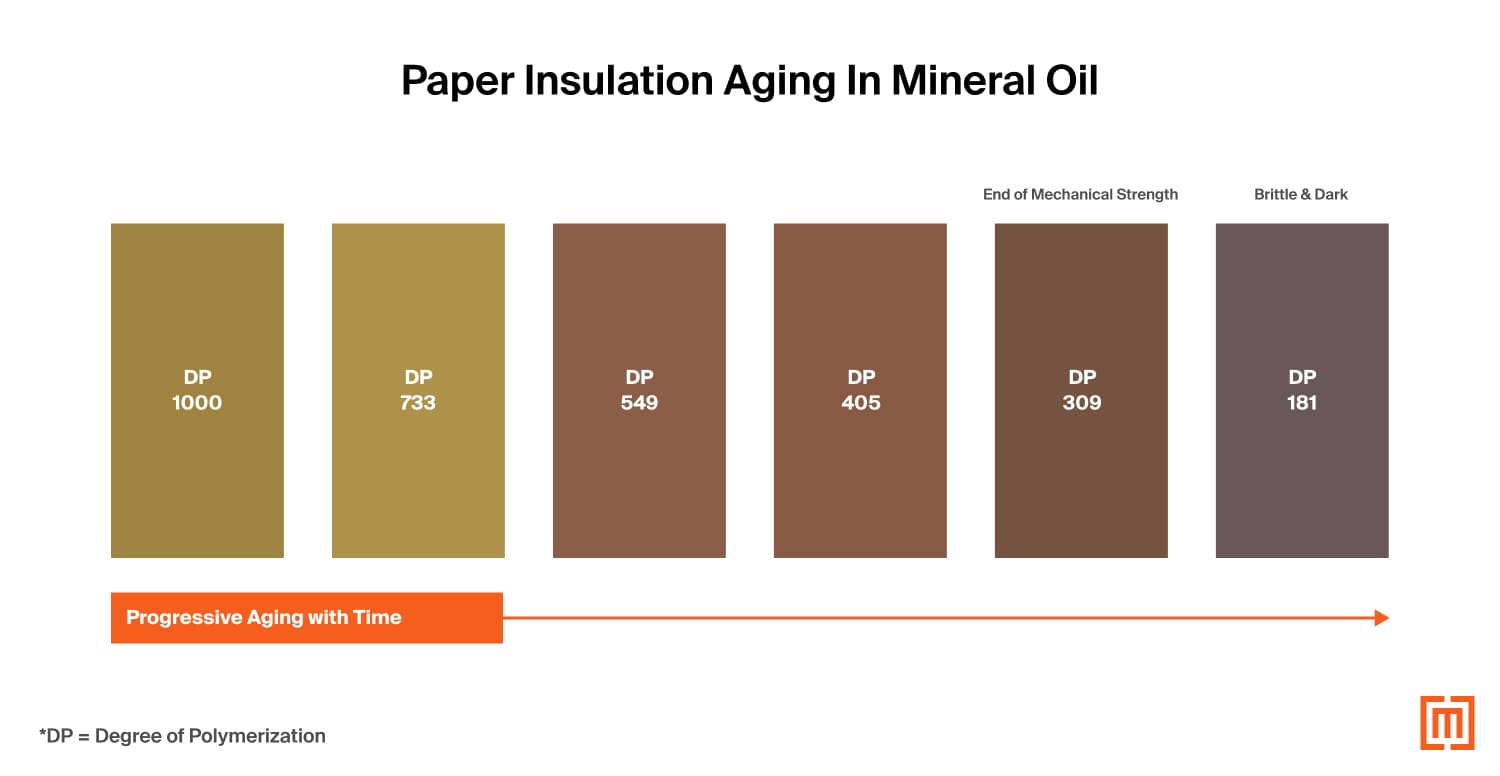
Cellulose paper can be chemically treated to offer higher thermal properties above 105°C.
Thermally-Upgraded Kraft Paper
Thermally-upgraded kraft paper (TUK) is also 100% made from kraft wood pulp. The paper is chemically treated, however, to reduce decomposition under elevated temperatures. TUK is also more durable than untreated kraft paper. It provides more stress tolerance and is less prone to breaking. Transformers with TUK usually have a 65°C (or 55/65°C) temperature rise. 65°C temperature rise units with TUK offer an insulation class rating of 120°C.
The use of TUK paper with a 55°C temperature rise offers 12% continuous overload capacity for oil-filled transformers.
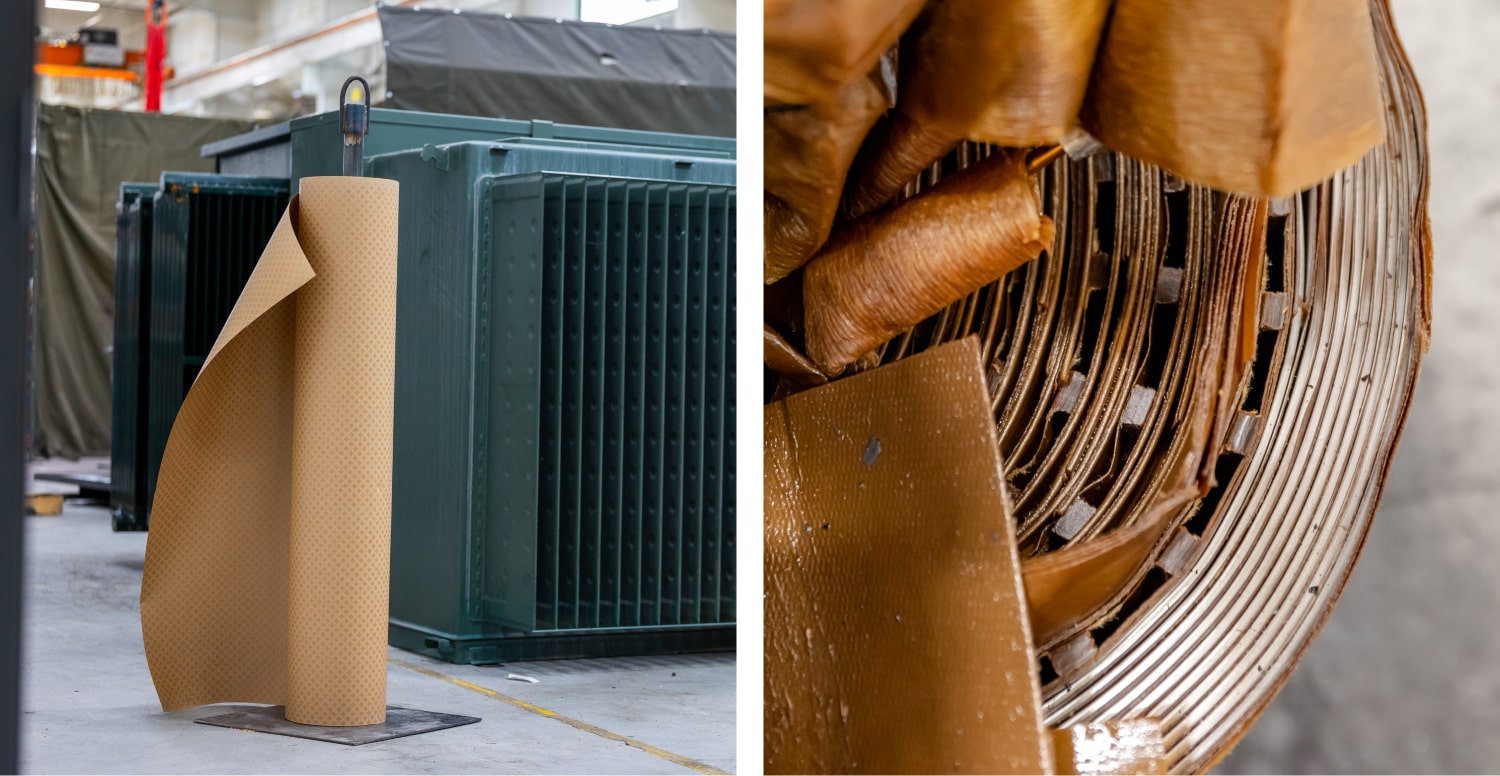
Liquid
Mineral Oil
Mineral oil is the standard fluid used in conjunction with cellulose paper insulation. It has been the standard insulating fluid used for many years. Of all insulating fluids, mineral oil has the most historical data available.
Natural Ester Oil
Natural Esters (FR3® fluid) provide a 100% biodegradable alternative as well as higher flashpoint. Natural esters also break down moisture through hydrolysis. This can offer extended life of the cellulose insulation paper. Natural esters also offer higher thermal capabilities with solid insulation materials.
Standard Temperature Ratings in Liquid-Filled Transformers
The table below shows the different temperature characteristics for solid and liquid insulating materials.
Dry-Type Insulating Mediums
Dry-type transformers use solid materials to insulate the winding conductors. Instead of oil, the air surrounding the coils provides cooling. For this reason, dry-type transformers run at much higher temperatures. Their thermal capabilities must be higher than liquid types. (Learn about transformer cooling classes)
Early dry transformer coils offered an 80°C temperature rise. Later, 115°C ratings used synthetic insulating materials like silicon and asbestos. The disuse of asbestos led to the development of aramid fibers. Aramid paper was originally developed under the trade name Nomex. It is the most common insulation medium for dry-types to date.
Solid Insulation
Aramid Paper
Aramid paper is made up of durable, heat-resistant fibers. It offers higher thermal characteristics for transformer insulation. Standard aramid paper designs allow for a 220°C insulation class. This allows for a higher hotspot temperature of 180°C above ambient.
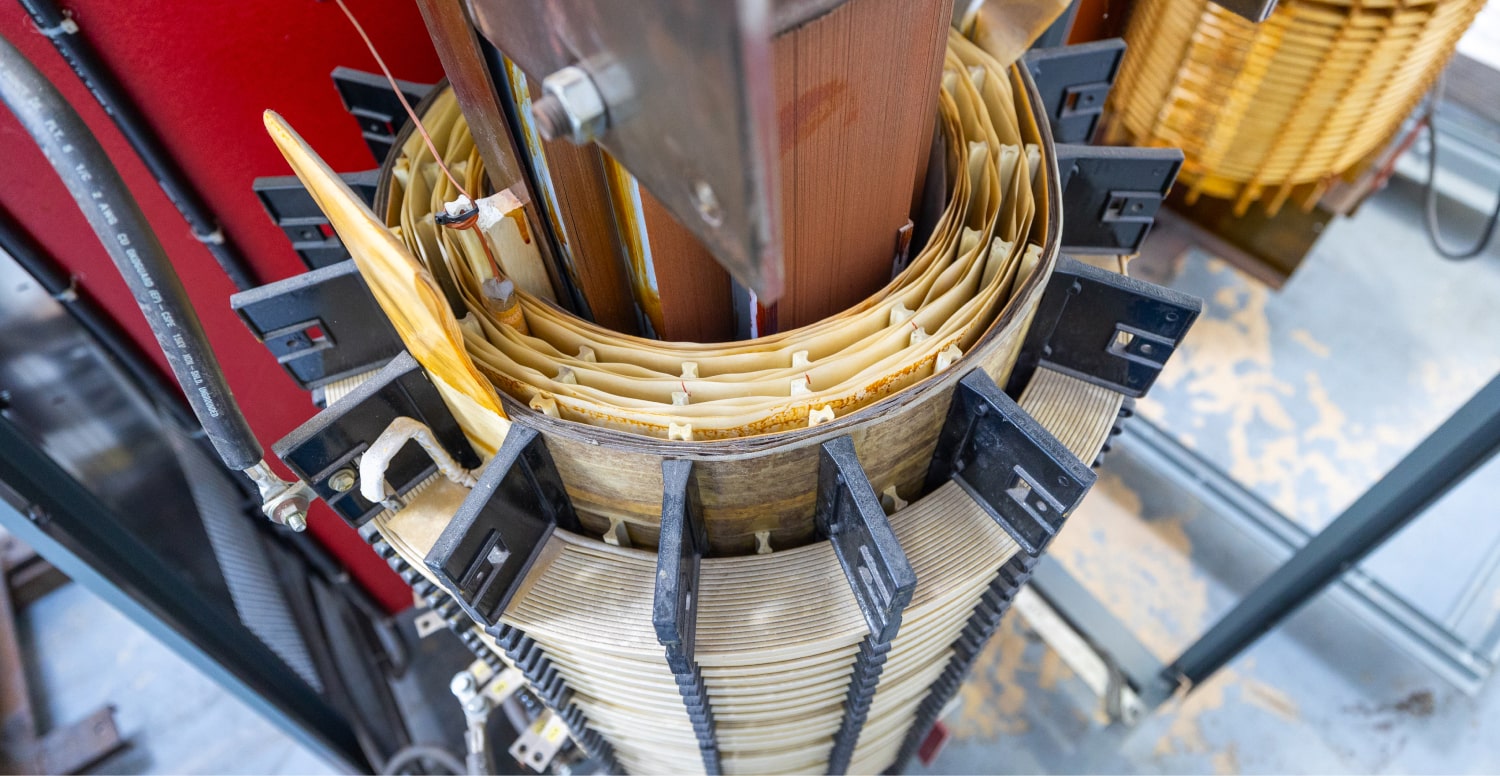
Cast Resin
Cast resin is another suitable solid insulation medium for dry windings. The entire winding assembly is cast in an epoxy resin mixture. The cast resin around the windings seals them from moisture and dirt. This reduces maintenance. Cast resin has a lower tolerance for heat than aramid insulation. For this reason, cast resin transformers will have a lower insulation class rating. An average winding temperature rise of 80°C or 115°C is typical.
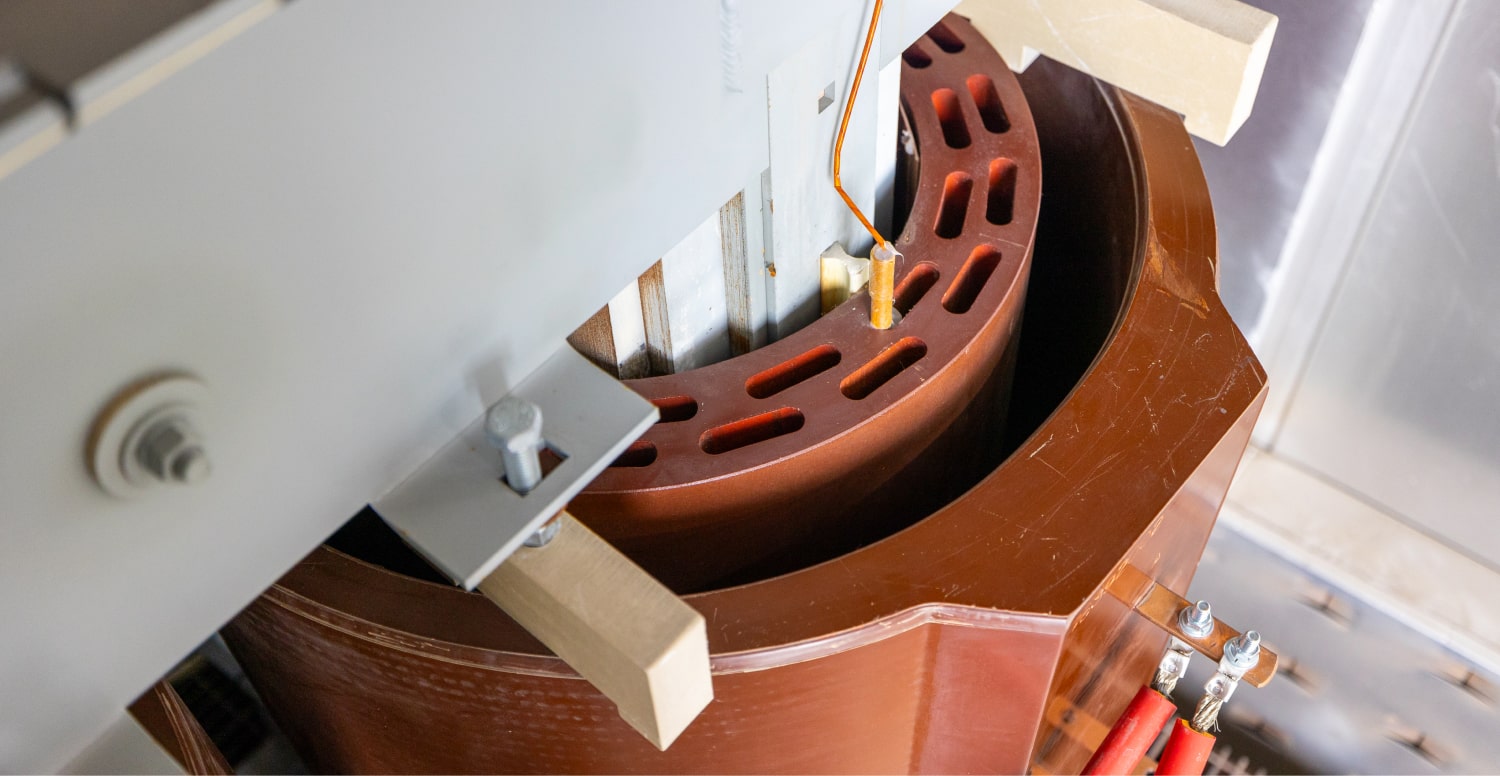
Common Temperature Ratings in Dry-Type & Cast Resin Transformers
*Alternate 80°C or 115°C ratings may be used.
Alternate Temperature Rise Ratings & Overload Capability
You may have noticed that earlier insulation mediums required more conservative temperature thresholds. For example, neutral kraft paper used a temperature rise of 55°C in oil-filled transformers. Early dry-type insulation systems were designed with an 80°C temperature rise. This was due to the thermal limitations of the insulation systems available at the time. When a design uses the same lower AWR with higher temperature rated insulating materials, you gain three possible advantages:
- Overload capacity
- Longer life-expectancy
- Increased efficiency
Overload Capacity
Most manufacturers offer a 220°C insulation class with standard dry-type designs. Such designs usually come with a 150°C temperature rise. This leaves no additional capacity at full load. At a max ambient of 40°C, the hotspot temperature of the coils under full load would be 220°C. Designing a lower temperature rise rating will reduce the hotspot temperature. This increases the thermal (loading) capacity of the windings. The hotspot temperature for an 80°C temperature rise would be 150°C at full load. This offers 47% continuous overload capacity. A 115°C temperature rise would offer 19% continuous overload.
Forced air ratings add 33% overload capacity to a transformer. But, fan ratings do not offer continuous overload capability. This is the advantage of lower winding temperature rises.
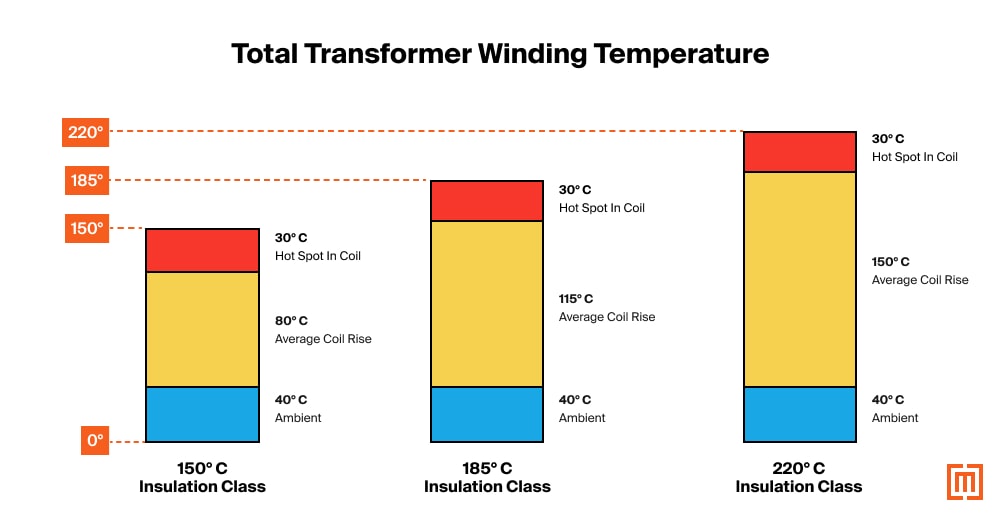
Longer Life Expectancy
Reducing the hotspot temperature reduces the thermal stress on the winding insulation. The result is that the insulation will degrade much slower over time. This can improve the standard life expectancy of a transformer.
Increased Efficiency
Transformers are very efficient. But, they do not run at peak efficiency under heavy load. The additional load capacity of an 80°C or 115°C temperature rise also translates into a higher efficiency. Increased loading capacity helps move transformers closer to the efficiency sweet spot (~50%).
The increased load capacity, lifespan, and efficiency gains of a lower temperature rise may pay dividends in the future. A standard 150°C rating will save you some up front cost. But, it may not always be the best option for your project.
Conclusion
Understanding your transformer’s temperature ratings and thermal capabilities is key to seeing a long service life from your unit. Please reach out to us with additional questions about temperature ratings and design options for your transformer.